CNC Lathe Machine Parts Name: Understanding Their Importance in Metal Fabrication
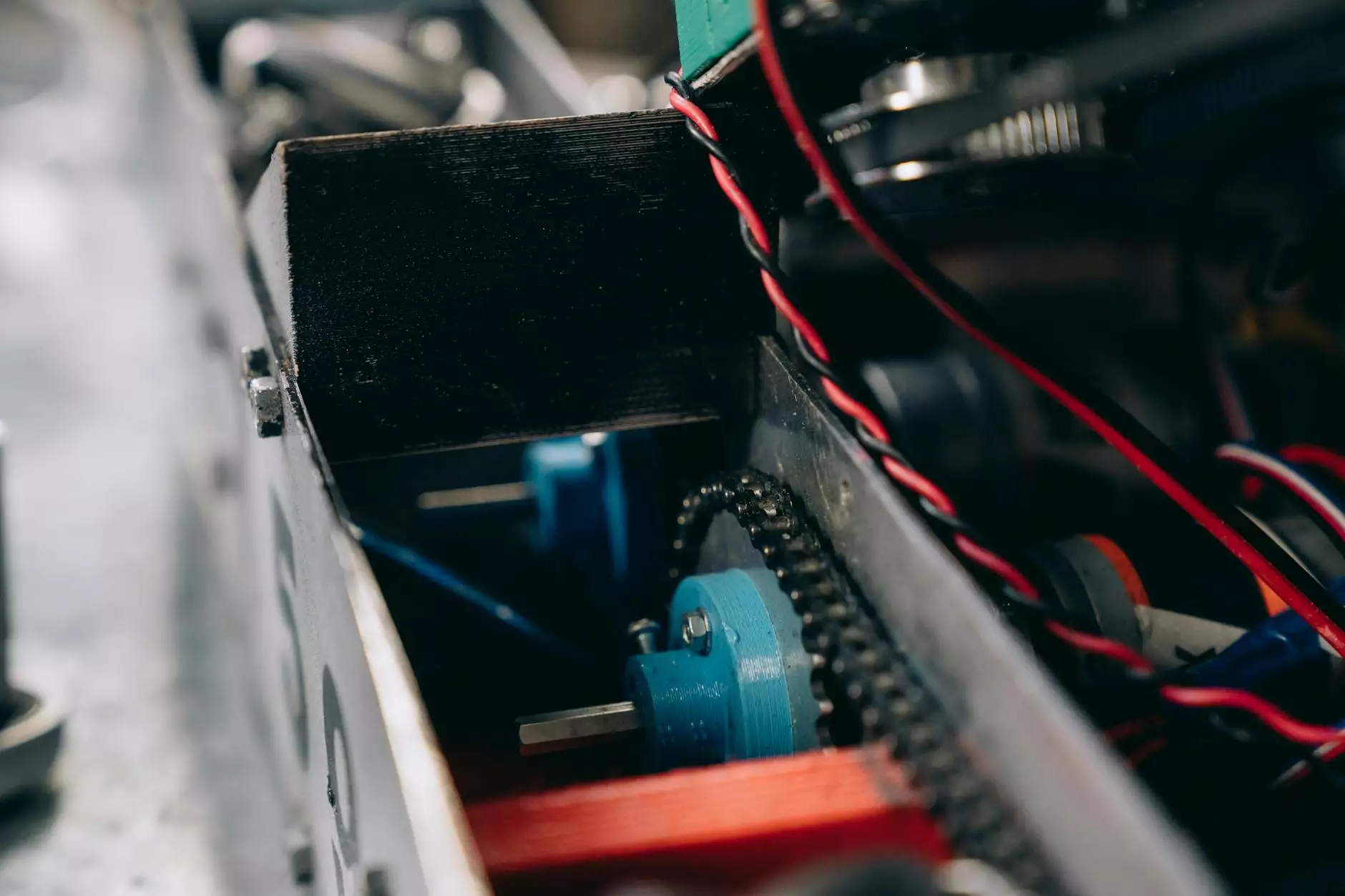
The CNC lathe machine plays a pivotal role in the manufacturing sector, particularly in metal fabrication. It is essential to comprehend the various parts that make up a CNC lathe and how they contribute to machining efficiency and precision. This article aims to present a detailed overview of the cnc lathe machine parts name, their functions, and their importance in modern metalworking practices.
What is a CNC Lathe Machine?
A CNC lathe machine is a computer-controlled machining tool that uses rotational movement to shape material into precise objects. The term "CNC" stands for Computer Numerical Control, which allows for the automation of manufacturing processes. By programming the lathe with specific parameters, manufacturers can achieve consistent and intricate designs that are otherwise challenging to produce manually.
The Structure of a CNC Lathe Machine
Understanding the structural components of a CNC lathe machine is critical for anyone involved in metal fabricators. Below are the main parts of a CNC lathe machine:
- Bed: The foundational component that supports all other parts of the lathe.
- Saddle: Moves horizontally along the bed and supports the cutting tool.
- Headstock: Houses the spindle, which rotates the workpiece; it includes gears and drive mechanisms.
- Tailstock: Positioned opposite the headstock, it provides additional support for longer workpieces.
- Tool Post: Secures the cutting tools in place during operation.
- Spindle: The rotating axis that holds and drives the workpiece.
- Chuck: A clamping device that secures the workpiece onto the spindle.
- CNC Control System: The brain of the machine, allowing operators to input designs and specifications.
- Power Supply: Provides the necessary energy for the lathe's operation.
- Carriage: Supports the cutting tool and is responsible for moving it along the workpiece.
Detailed Descriptions of CNC Lathe Machine Parts
1. Bed
The bed is the core structure of the CNC lathe. It is made from solid cast iron or steel, designed to absorb vibrations and maintain stability during operation. A well-built bed ensures precision machining as it minimizes deflections and maintains alignment throughout the cutting process.
2. Saddle
The saddle is a sliding component that travels on the bed, allowing for lateral movement of the cutting tool. Equipped with guideways, it maintains a smooth operation. The saddle's movement is crucial for achieving the desired depth and angle during the cutting process.
3. Headstock
The headstock encloses the spindle and serves as the drive mechanism for rotating the workpiece. Inside the headstock, you’ll find gears and pulleys that help control the speed and torque of the spindle, allowing operators to adjust settings suitable for specific materials and cutting requirements.
4. Tailstock
Opposite the headstock, the tailstock provides support for the workpiece, especially for longer pieces that require additional stability. It can be adjusted horizontally and often includes a live center for precise alignment.
5. Tool Post
The tool post is where the cutting tools are clamped securely. There are various types of tool posts, including fixed and rotary, allowing for different machining strategies. The correct selection and maintenance of the tool post are essential for effective and accurate cutting.
6. Spindle
The spindle serves as the active component that rotates the workpiece at various speeds determined by the job's specific needs. Precision bearings within the spindle are critical for maintaining its operational accuracy and longevity.
7. Chuck
The chuck is a specialized device that grips the workpiece firmly. Different types of chucks, such as three-jaw and four-jaw chucks, cater to different shapes and sizes of workpieces. Properly securing the workpiece is vital for safety and precision.
8. CNC Control System
The CNC control system dictates how the lathe operates. It receives the design specifications from the operator and ensures that each component of the lathe responds accordingly. Software updates and proper system calibration are essential for maintaining accuracy and efficiency.
9. Power Supply
A reliable power supply is necessary for any CNC lathe to function efficiently. The power supply provides the energy needed for all components, including motors and the CNC control system.
10. Carriage
The carriage holds the cutting tool and positions it against the workpiece. It moves in precise increments according to the programmed machining path, allowing for complex shapes to be formed accurately and efficiently.
Importance of CNC Lathe Machine Parts
Each component of a CNC lathe machine plays a crucial role in achieving the desired manufacturing outcomes. The efficiency and effectiveness of these parts directly impact:
- Precision: High-quality components lead to tighter tolerances and better final products.
- Speed: A well-maintained lathe can operate at faster speeds, reducing overall production time.
- Durability: Using robust parts ensures that the lathe can withstand heavy workloads over time.
- Flexibility: CNC technology allows for quick changes in machining tasks, accommodating various production runs.
Common Applications of CNC Lathe Machines
CNC lathe machines are utilized across various industries due to their adaptability and precision. Here are some common applications:
- Aerospace Manufacturing: Producing components like turbine blades and landing gear.
- Automotive Industry: Machining parts such as engine blocks, drive shafts, and bushings.
- Medical Devices: Creating precision tools and implants that require stringent quality controls.
- Electronics: Manufacturing housings, connectors, and other intricate components.
- Architectural Elements: Producing decorative features and structural supports.
The Future of CNC Lathe Machines
As the industry evolves, so too does the technology around CNC lathe machines. Innovations such as smart manufacturing and the integration of artificial intelligence are paving the way for enhanced operational efficiencies and capabilities.
1. Smart CNC Technology
Smart CNC machines equipped with IoT technology can provide real-time data analytics, allowing for predictive maintenance and enhanced performance monitoring. This technology enables manufacturers to remain agile in an ever-changing market.
2. Automated Systems
The future of machining includes fully automated CNC systems that operate with minimal human intervention. This trend not only reduces labor costs but also increases safety in manufacturing.
3. Sustainability Practices
With a growing focus on sustainability, CNC lathe machines are being designed to minimize waste and improve energy efficiency. This shift not only helps the environment but also lowers operational costs.
Conclusion
Understanding the various cnc lathe machine parts name is essential for anyone in the metal fabrication industry. As technology advances, so does the importance of these components, influencing precision, speed, and overall manufacturing efficacy. Investing in high-quality lathe parts not only enhances performance but also ensures longevity and reliability in machining processes.
Ultimately, as industries continue to demand high-quality components and efficient production methods, having a solid grasp of CNC lathe technology will remain a vital asset for manufacturers. Whether you're a seasoned professional or new to the field, leveraging the full potential of a CNC lathe machine can lead to significant competitive advantages in today's fast-paced manufacturing environment.