Injection Molding Manufacturing: Transforming Ideas into Reality
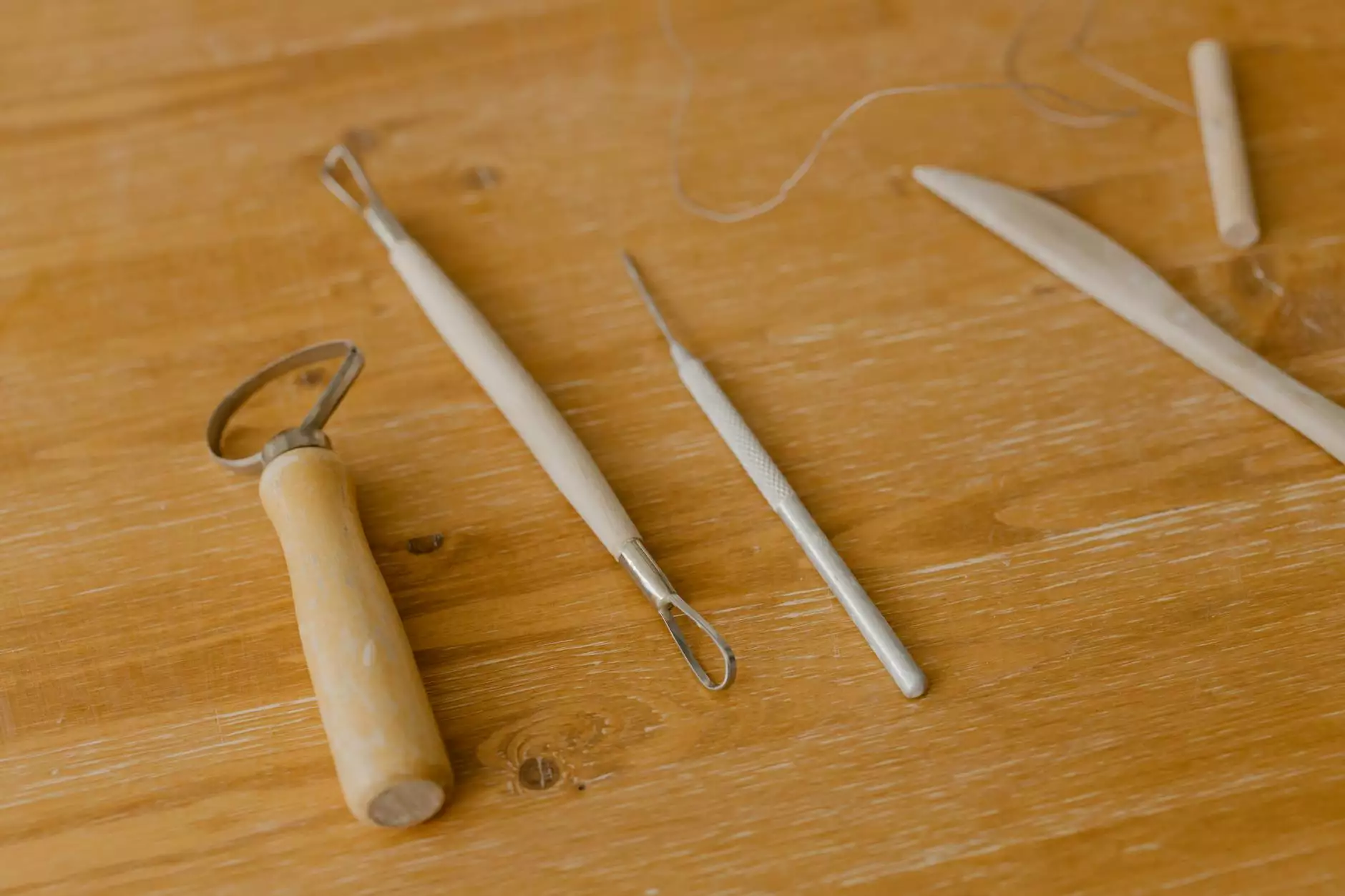
In today's rapidly evolving industrial landscape, injection molding manufacturing has emerged as a game-changer, driving efficiency and precision across various sectors. This article delves into the intricacies of injection molding, exploring its benefits, processes, applications, and future trends. Whether you are a seasoned professional in the manufacturing domain or a business owner considering adopting this technology, understanding injection molding can significantly enhance your production capabilities.
What is Injection Molding?
Injection molding is a manufacturing process used to produce parts by injecting molten material into a mold. The process is highly versatile and can accommodate various materials, including plastics, metals, and even ceramics. It is widely utilized in numerous industries, including automotive, medical, consumer products, and electronics. With its ability to create complex shapes with high precision, injection molding has become a staple in modern manufacturing.
The Injection Molding Process
The injection molding process consists of several crucial steps:
- Material Preparation: The process begins with preparing the raw materials, typically plastic pellets, which are heated until they become sufficiently molten.
- Mold Creation: A mold is designed and manufactured based on the specifications of the desired part. This mold is usually made from steel or aluminum to withstand high pressures.
- Injection: The molten material is injected into the mold under high pressure. The speed and consistency of this injection are critical for achieving a uniform product.
- Cooling: Once the mold is filled, the material is allowed to cool and solidify. This cooling phase is vital for ensuring dimensional accuracy.
- Demolding: After cooling, the mold opens to release the finished part. The cycle can be repeated for mass production.
Benefits of Injection Molding Manufacturing
There are numerous advantages associated with injection molding manufacturing. Here are some of the key benefits:
- High Efficiency: The automated nature of injection molding allows for rapid production cycles, making it ideal for high-volume manufacturing.
- Cost-Effective: Despite the initial setup costs, the per-unit cost decreases significantly with higher production numbers, leading to substantial savings.
- Precision and Accuracy: Injection molding can create intricate designs and components with tight tolerances, ensuring high-quality products.
- Material Versatility: This process can utilize a wide range of materials, including various thermoplastics and thermosetting polymers.
- Reduced Waste: The design of the injection molding process minimizes waste material, making it an environmentally friendly option.
Applications of Injection Molding Manufacturing
Injection molding is prevalent across several industries. Some of its most notable applications include:
1. Automotive Industry
In the automotive sector, injection molding is used to manufacture a wide range of components, from dashboard panels to intricate engine parts. Its ability to produce lightweight and durable parts contributes to improving fuel efficiency while maintaining safety standards.
2. Medical Devices
The medical industry relies heavily on injection molding for producing precision instruments, syringes, and other devices. The process enables manufacturers to create sterile, disposable products that meet the stringent regulatory requirements of the healthcare field.
3. Consumer Products
From household items like containers and toys to electronics and packaging, injection molding plays a vital role in the consumer goods market. The ability to customize colors and textures allows brands to deliver products that resonate with consumers.
4. Industrial Components
Many industrial applications utilize injection-molded parts, such as gears, housings, and various assemblies. These components must be durable and reliable, and injection molding delivers both.
Technological Advances in Injection Molding
The injection molding industry is continually evolving, driven by technological advancements aimed at enhancing efficiency and reducing costs. Some key innovations include:
1. 3D Printing for Molds
Integrating 3D printing technology into mold making allows for faster prototyping and reduced lead times. Manufacturers can create complex molds with intricate designs that were previously difficult or impossible to achieve.
2. Smart Manufacturing and IoT
The Internet of Things (IoT) is revolutionizing injection molding manufacturing by enabling real-time monitoring of machines and processes. This data-driven approach allows for predictive maintenance, reducing downtime and improving overall productivity.
3. Advanced Materials
New materials such as biodegradable plastics are being developed for use in injection molding, addressing environmental concerns and expanding the range of applications for molded parts.
Quality Control in Injection Molding Manufacturing
Ensuring high quality in injection molded parts is critical to success. Here are some measures taken to uphold quality standards:
- Regular Maintenance: Routine checks and maintenance of molding machines are crucial for maintaining precision and avoiding defects.
- Testing and Inspection: Finished products undergo various tests, including dimensional checks and stress testing, to ensure they meet specifications.
- Training and Expertise: Employing skilled professionals who understand the intricacies of the injection molding process ensures better control over quality.
Environmental Considerations in Injection Molding
As industries strive for sustainable practices, injection molding manufacturing is also adapting. Here are ways the process can be made more environmentally friendly:
- Use of Recyclable Materials: Utilizing recyclable thermoplastics reduces the consumption of raw materials.
- Energy Efficiency: Newer injection molding machines are designed to consume less energy, further decreasing the environmental impact.
- Waste Management: Companies are implementing better waste management practices to minimize scrap and improve recycling processes.
Future Trends in Injection Molding Manufacturing
The future of injection molding manufacturing looks promising, with several trends on the horizon:
- Increased Automation: Automation technologies will continue to evolve, streamlining the manufacturing process and further reducing cycle times.
- Customization: As consumer demands for personalized products grow, injection molding will adapt, allowing for customizable features in designs and materials.
- Integration with AI: Artificial intelligence will play a role in optimizing injection molding processes, improving predictive maintenance, and increasing operational efficiencies.
Conclusion
In summary, injection molding manufacturing is at the forefront of industrial innovation, offering unparalleled benefits in terms of efficiency, precision, and sustainability. As industries continue to evolve, the role of injection molding will only expand, providing businesses with the tools they need to meet modern manufacturing demands. Embracing this technology not only enhances product quality but also paves the way for a more sustainable and efficient industrial future.
For more detailed information and high-quality injection molding solutions, visit deepmould.net today.